La logistica è il settore che, più di ogni altro, ha subito un’innovazione significativa, trasformando radicalmente il suo elemento più caratteristico: il magazzino. Questa trasformazione ha coinvolto non solo l’aspetto e la connotazione tecnologica, ma anche le modalità di gestione. Tale trasformazione è stata accompagnata da cambiamenti significativi nelle infrastrutture impiantistiche che hanno dovuto supportare l’elettrificazione e la connettività necessarie per consentire l’introduzione massiccia dell’automazione avanzata.
Il settore della logistica negli ultimi anni ha subito profondi mutamenti. L’impulso dato dalla pandemia e dal conseguente lockdown ha portato alla crescita esponenziale dell’e-commerce con la naturale esigenza di potenziare ogni singolo segmento della supply chain: quello dei trasporti, divenuti nel tempo sempre più precisi e capillari, ma anche quello dei magazzini, divenuti sempre più bisognosi di spazio e di tecnologia per la loro gestione.
Soffermandosi sull’aspetto statico della catena di distribuzione – ovvero il magazzino – è importante segnalare come il suo sviluppo stia interessando diversi comparti:
- l’immobiliare: con la costruzione di nuovi edifici per la logistica e con l’auspicabile riqualificazione “brown field” tesa, cioè, dare nuova vita ad aree urbane in passato utilizzate per attività industriali o commerciali per riconvertirle a fini logistici;
- l’impiantistico: con l’installazione di diverse tipologie di reti tecnologiche per l’utilizzazione di energia elettrica, segnali e fluidi;
- l’energetico: con l’installazione di centinaia di kW di potenza rinnovabile.
Inoltre, anche l’approccio ai servizi tecnici connessi alla gestione della supply chain è profondamente variato, basti pensare alla manutenzione che, all’attualità, deve ricorrere alle sue forme più evolute per garantire la continuità di servizio delle attività di magazzino.
Il magazzino degli anni ‘80
Fino a pochi decenni fa un magazzino era il luogo in cui accantonare le scorte di materie prime o semilavorati per le attività di intralogistica o di prodotto finito per la fase di distribuzione. Lo sforzo dei tecnici della logistica era quello di ottimizzare gli spazi per disporvi la merce da stoccare e consentire ai mezzi di movimentazione (carrelli elevatori e transpallet) e agli operatori un’agevole circolazione.
L’intera area del magazzino, quindi, veniva dedicata alla sistemazione dei prodotti organizzando il layout per la gestione delle fasi principali del processo logistico:
- ricevimento;
- stoccaggio;
- picking (prelevamento);
- movimentazione;
- spedizione.
La struttura edilizia del magazzino era progettata per soddisfare le esigenze delle diverse fasi operative e i requisiti igienico-sanitari fondamentali. Oltre alle vie di circolazione, l’unico spazio, di dimensioni minime, non destinato allo stoccaggio era occupato dal box ufficio utilizzato dal responsabile del reparto o, nelle aziende più strutturate, dai capireparto per le attività gestionali e organizzative.
L’altezza interna dell’edificio, normalmente, non era mai inferiore a 7 metri e solitamente arrivava anche a 12 metri per consentire elevate densità di stoccaggio.
Gli impianti nei magazzini
Dal punto di vista impiantistico, le risorse destinate al magazzino erano limitate all’essenziale. L’illuminazione ordinaria non doveva garantire elevati livelli di illuminamento: 100 lux nelle aree di stoccaggio (che potevano salire a 200 lux se occupate con continuità) e 300 lux nelle aree di trasporto, imballaggio e spedizione.
Nei magazzini con scaffali, l’illuminamento medio richiesto scendeva a 20 lux per le zone di passaggio e a 150 lux per le aree di passaggio con presenza di personale e per le sale di controllo. I punti di prelievo della forza motrice da destinare ad attività di manutenzione andavano posizionati con estrema attenzione in quanto, nei periodi di maggiore stipamento dei locali, rischiavano di essere occlusi e/o danneggiati dai prodotti movimentati e stoccati.
Le aree dedicate all’alimentazione dei sistemi di ricarica delle batterie al piombo-acido dei carrelli elevatori e dei transpallet elettrici, quando presenti, erano (e sono tuttora) concentrate in zone ben delimitate, spesso all’esterno. Questo perché il processo di ricarica prevede l’emissione di idrogeno, che può creare atmosfere potenzialmente esplosive, richiedendo quindi un’adeguata ventilazione.
Gli impianti speciali asserviti al magazzino prevedevano, neanche a dirlo, dotazioni spartane: oltre alle linee telefonica e dati per il box/ufficio e ai sistemi dedicati alla security (impianto antintrusione) e alla safety (impianto rivelazione e allarme incendi, quando previsti dalle normative di Prevenzione Incendi), difficilmente emergevano altre esigenze.
Ovviamente, a richieste così “minimal” in termini di numero e tipologia di utenze da alimentare, non potevano che corrispondere requisiti standard in termini di qualità dei parametri elettrici di fornitura.
Un’analoga impostazione veniva mantenuta per gli impianti a fluido. Gli ambienti non erano climatizzati, dato che la presenza degli operatori era saltuaria e intermittente, e questi erano comunque in movimento. La salubrità dell’aria era garantita dai ricambi con l’esterno ottenuti tramite aperture di ventilazione, normalmente ricavate in alto nelle pareti di tamponamento o direttamente nella copertura a shed, oppure, in caso di pericoli legati alla particolare merce, mediante ventilazione meccanica.
A fini di sicurezza, se previsti dalla normativa di Prevenzione Incendi, poteva essere presente l’impianto di spegnimento a idranti (interno e/o esterno) e/o quello a sprinkler a seconda del livello di intensità dello stoccaggio della merce.
I magazzini oggi: una vera supply-chain
La situazione attuale è radicalmente cambiata, soprattutto per quanto riguarda le reti tecnologiche elettriche ed elettroniche. Questo perché gli impulsi forniti dagli avvenimenti citati in apertura di articolo hanno spinto il settore logistico a potenziare ogni singola fase della supply chain e ciò è stato possibile grazie all’automazione avanzata che ha portato alla diffusione di:
- WMS (Warehouse Management System): è un sistema software che ha il compito di supportare la gestione operativa dei flussi fisici che transitano per il magazzino;
- identificazione avanzata: le tecnologie radio sono utilizzate per identificare gli articoli presenti in un magazzino;
- tecnologie di smistamento automatico: Sorter, Bomb Bay, Cross Belt, Tilt Tray, Shoe Sorter, Pounch Sorter sono diversi sistemi automatici di smistamento di pezzi o colli tramite nastri trasportatori, deviatori di direzione, vassoi a deflessione;
- tecnologie di picking automatico: le postazioni di prelievo (baie) sono dotate di robot antropomorfi, cartesiani e umanoidi a cui demandare i compiti ripetitivi di prelevamento e di posizionamento sui punti di imballaggio o di trasporto e smistamento;
- tecnologie di movimentazione automatica avanzata: gli AGV (Automated Guided Vehicle) sono robot per la movimentazione di pezzi, colli o interi supporti di stoccaggio (POD) che seguono un percorso fisso, rilevato da sistemi guidati e si fermano in caso di ostacoli; gli AMR (Autonomous Mobile Robots) sono robot mobili che si muovono autonomamente in un ambiente senza un’infrastruttura guidante fissa a pavimento;
- trasloelevatori o miniload: sistema di stoccaggio e prelievo automatizzato per unità di carico di piccole o medie dimensioni come cassette, cartoni, vassoi. È costituito da una serie di corridoi con scaffalature a singola o doppia profondità, all’interno dei quali operano delle macchine automatizzate in grado di eseguire contemporaneamente movimenti lungo l’asse orizzontale e lungo l’asse verticale.
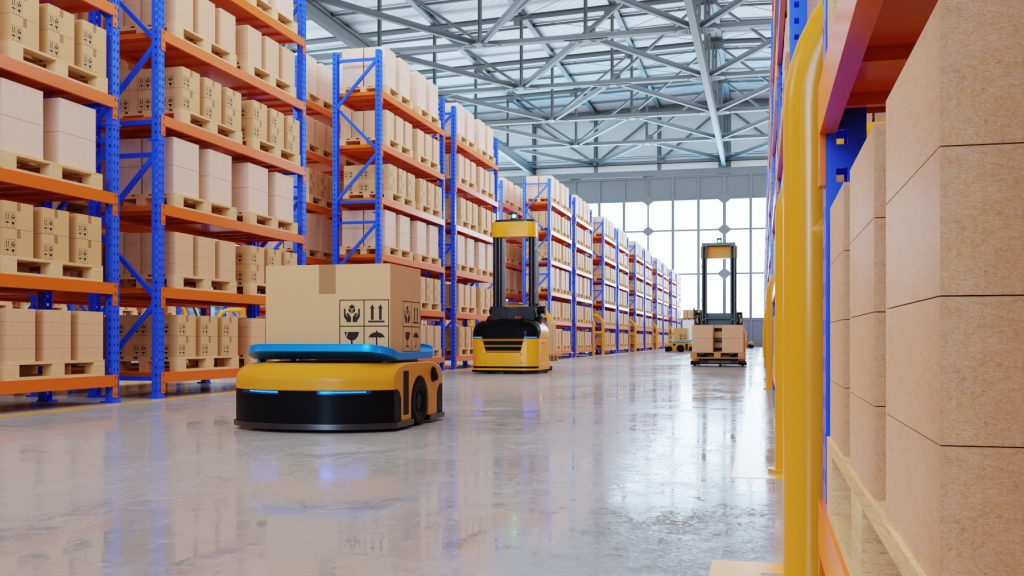
Come è facile intuire, non tutti i magazzini sono dotati di tutte le tecnologie appena indicate: la scelta tecnologica è il fattore chiave dello sviluppo e va effettuata attentamente esaminando aspetti quantitativi e qualitativi, la selettività, l’accessibilità, l’espandibilità, la scalabilità, la ridondanza.
Al netto di ciò, è indubbio che tali tecnologie, anche se parzialmente adottate, abbiano cambiato in maniera marcata le esigenze impiantistiche di un magazzino di ultima generazione.
I carichi elettrici moltiplicati
Esaminando i carichi elettrici, si nota una proliferazione significativa accompagnata da un aumento della potenza impegnata. Sono principalmente costituiti da motori elettrici con i relativi azionamenti, ovvero carichi induttivi e non lineari che assorbono energia reattiva e distorcono la forma d’onda della tensione di alimentazione.
Inoltre, la gestione automatica dei diversi sistemi tramite PLC e la loro supervisione richiedono una particolare attenzione alla qualità dell’alimentazione elettrica, sia in termini di forma d’onda che di continuità del servizio. Oltre a ciò, molti magazzini hanno optato per l’elaborazione in sede degli ordini telematici e delle relative fasi di evasione, dotandosi di una significativa potenza di elaborazione.
Questo spesso porta alla realizzazione di piccoli data center, che rappresentano carichi elettrici particolarmente critici in termini di qualità dell’alimentazione elettrica.
L’impianto elettrico utilizzatore e gli impianti speciali
L’impianto elettrico utilizzatore asservito al magazzino di nuova generazione, quindi, si è dovuto adattare alle nuove specifiche: i cablaggi e le vie cavo sono aumentati, i quadri elettrici hanno assunto dimensioni più importanti, i sistemi di protezione da sovratensioni di origine atmosferica sono sempre più presenti così come i sistemi di rifasamento dedicati e i dispositivi di filtraggio delle componenti armoniche.
La progettazione dell’impianto elettrico utilizzatore di un magazzino è diventata una pratica professionale complessa e coinvolgente, al pari di quella di un reparto produttivo.
Anche gli impianti speciali, ovviamente, hanno dovuto supportare la rivoluzione 4.0 della supply chain: in particolare, gli impianti di trasmissione dati, sia in modalità cablata sia wireless, sono diventati protagonisti delle installazioni all’interno di un magazzino.
Infatti, com’è noto, senza le comunicazioni elettroniche l’automazione sarebbe ferma alla fine degli anni ’60 quando, cioè, il PLC entrò in fabbrica; non si parlerebbe, quindi, di Quarta Rivoluzione Industriale e di Industrial Internet of Things (IIoT), quest’ultimo l’applicazione dell’IoT al settore industriale.
Questo costituisce il cuore dell’innovazione digitale: la convergenza tra tecnologia operativa (OT) e tecnologia dell’informazione (IT). La prima si occupa dell’uso di hardware e software per monitorare processi fisici, dispositivi e infrastrutture, mentre la seconda si concentra sul controllo dei dati per garantirne riservatezza, integrità e disponibilità. Con l’integrazione IT-OT, i dati raccolti dalle apparecchiature fisiche e dai dispositivi IIoT possono essere utilizzati per identificare problemi e aumentare l’efficienza dell’intero sistema.
Nulla di tutto questo sarebbe possibile senza un’infrastruttura di rete robusta, flessibile e scalabile, capace di creare il tessuto neuronale dell’automazione avanzata. Per questo motivo, l’approccio alla progettazione della “rete di magazzino” non può più essere svolto con la stessa disinvoltura di qualche anno fa.
È necessario occuparsi del cablaggio, della distribuzione wireless, dei protocolli di rete e della relativa diagnostica, dell’integrazione dei sistemi e della sicurezza informatica. Appare evidente come ciò debba invogliare i professionisti verso team di progettazione multidisciplinari.